How Plant Technology is Meeting Increasing Demand for More Asphalt Products?
The new demands in the paving business, such as the production of sustainable asphalt mixes, more economical mixes and mixes with greater durability, have an effect on the chain of inputs, projects and equipment.
As a result, asphalt plants are evolving significantly with the goal of producing both traditional and more complex mixes that require special inputs such as lime, cellulose fibers and modified asphalt. Likewise, productivity, efficiency and an economical approach are being increasingly prioritized in this space.
Three new technologies in the market are bringing further benefits to the quality of the asphalt mix and/or the optimization of the production process. These are the new systems developed for control over aggregate drying time, fuel and energy economy through a new combustion system, and technology that helps control the mixing time between the aggregates and asphalt binder.
Control over aggregate drying time
To produce a cohesive mix with suitable properties for hot mix asphalt production, the aggregates must be completely dry and heated to obtain adhesiveness with the asphalt binder.
Aggregates from the same region may also have quite distinct characteristics, such as different water absorption capacity and adhesiveness with the asphalt binder.
Traditional plants dry and heat the aggregates in a rotating drum driven by motors with fixed speed. Subsequently, the drying time is fixed, regardless of the aggregate’s characteristics.
A new concept for an asphalt plant drying system was developed in order to adjust the aggregate drying time according to the characteristics of those inputs, in regards to adhesiveness and moisture absorption.
Intelligent combustion system in closed loop
Traditional asphalt plant burners use the air from the environment (sucked in by an exhaust fan with constant turning speed) and a mechanical fan (called a blower) to provide the amount of air needed for combustion inside the dryer drum. The control over the airflow for combustion is carried out by a component called the damper, placed in the gases’ outlet to the environment that controls the pressure of the plant by manipulating the gas flow. The optimum combustion ratio is 13:1 (13 volumes of air for one volume of fuel), and the airflow variation is dependent on the position of the damper since the exhaust flow is constant.
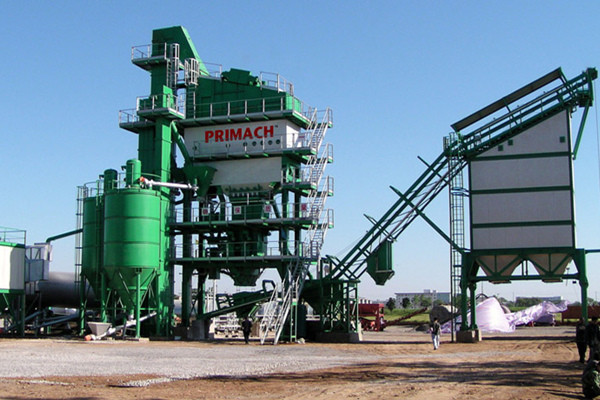